Aluminum composite sheet sealing steps
Things to Know about Aluminum composite sheet sealing steps
Sealing and filling seams (sealing) are among the principles of engineering and are an integral part of projects.
Air infiltration (cold and hot) and water into the building are the main reasons for reducing the comfort of residents.
This problem can exist in all new and old buildings and increases fuel consumption by up to 25%.
After designing and calculating the facade of the building, the sheets in the workshop are cut to the specified size
And the edges of all 2 cm cut sheets are bent into a box with a 90 degree angle.
And in any case, aluminum bending of 30 mm 30 mm 30 mm is created by riveting to connect the sheets to the structure.
The assembled sheets are finally spaced 1 cm apart on the adjacent sheet
And the substructure profiles are connected by a head screw.
In the same way, the other pre-assembled sheets are installed next to each other with the mentioned distance (1 cm on each side).
In the part where the facade should be executed in the form of an arch.
First, the sheets related to that part are cut and rolled with a specified rolling machine with a specified radius, and after assembly, it is ready to be installed on the substructure network.
After connecting all the sheets to the substructure, the sealing stage between the sheets, which is 1 cm, begins. In this stage, it can be sealed in several ways.
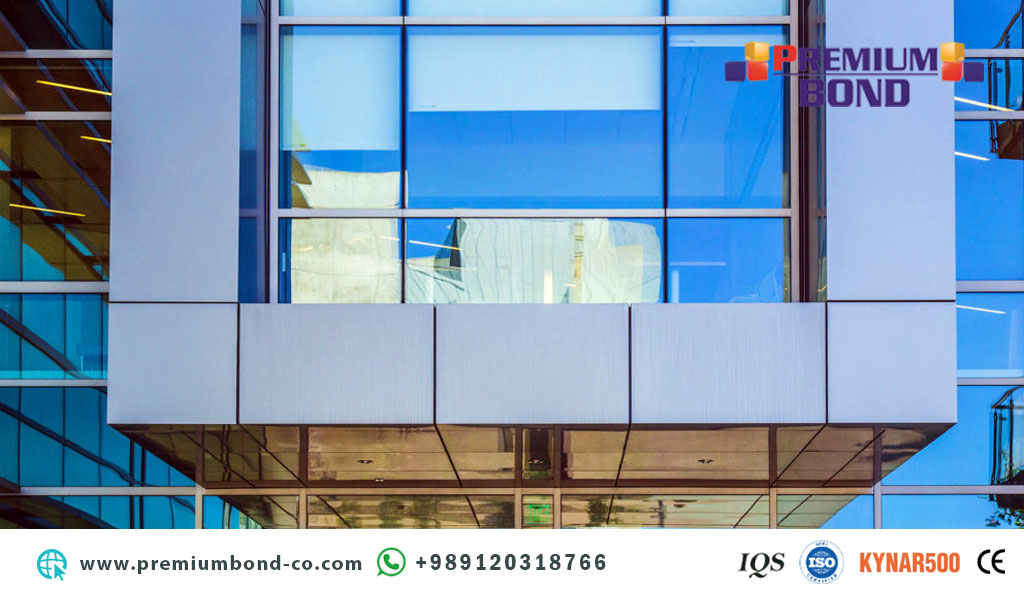
The steps for sealing composite aluminum sheets are as follows:
- Use PVC sealing tape
- Use foam and silicone glue
- Use a composite sheet belt
Each of which is described as follows:
1- Using PVC sealing tape
In this method, the strips that are ready in the market and made of PVC are easily covered by pressing these strips.
2- Using silicone foam and glue for sealing
In this method, solid foam foams with a diameter of 1.5 cm fill the seam depth by pressing inside the 1 cm seams and the remaining seams are filled with silicone glue.
3- Using belt buckles made of composite sheet for sealing
This method is the most correct and best method and is a collection of European details so that first the first sheet is installed, then the composite belt is installed on the corner of the previous sheet on the substructure and finally the side sheet is screwed under the belt and the facade is completely sealed.
Final level
This step involves removing and separating the protective label from the sheets. It should be noted that this label is covered in the final stage of sheet production in Premium bond plant in Iran. Sheet from the factory to after installation. Another advantage of using this cover is that you can specify the direction of use of all the sheets to one side with the arrow on which it is printed. Printing the name of the manufacturer on those sheets can also be a good advertisement.
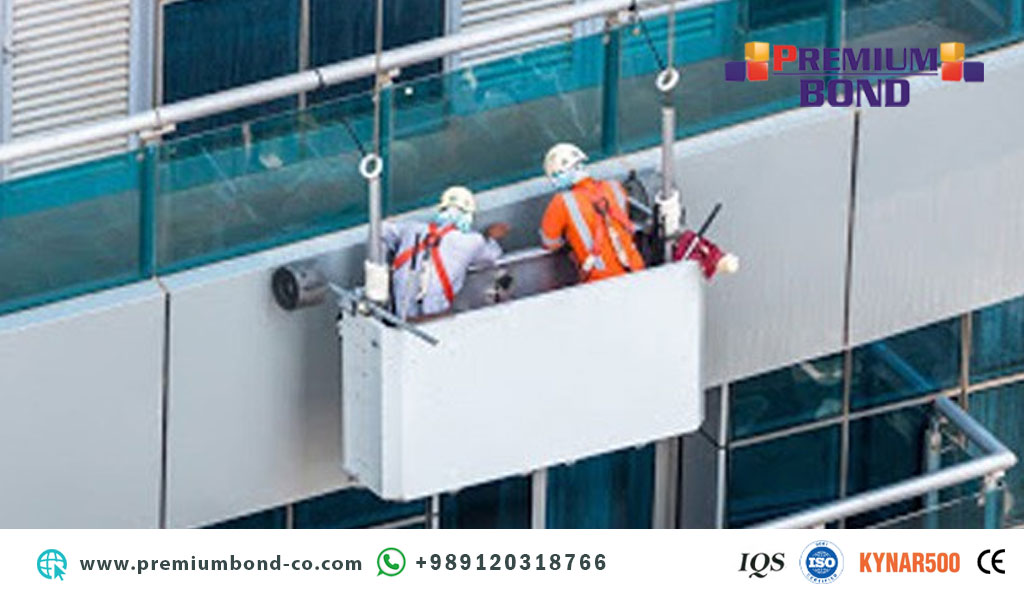
Leave a Reply