Anodized aluminum
What is the difference between Anodized or aluminum anodized?
Anodized aluminum has a thicker passive layer than naturally passivated aluminum, meaning it is more resistant to degradation and subsequent corrosion
Anodized aluminum is aluminum that has been treated to develop an exceptionally durable finish. To create anodized aluminum, you use an electrochemical process where the metal is immersed in a series of tanks, wherein one of the tanks, the anodic layer is grown from the metal itself
Aluminum also oxidizes under normal conditions So that in the presence of air and usually a layer of oxide is formed in a non-porous manner on the surfaces of aluminum parts.
Which is responsible for protecting the metal surface in the environment
However, the advantage of oxidation in the anodizing method over natural conditions is that it is more resistant to corrosion.
In anodizing aluminum anodizing or anodizing, the method of high resistance of Al2O3 aluminum oxide coating layer against corrosion, which is formed immediately on the surface of freshly cut aluminum, is used.
This layer is the natural corrosion resistance of this metal.
This layer, which is formed naturally,
It is very thin, sticky and protective.
Anodizing is actually a kind of thickening of the oxide layer to a thickness of several thousand times the thickness of the natural oxide layer.
The result is a hard layer with a thickness of about 25.5 microns over the entire aluminum surface, which is strong enough to withstand corrosion and abrasion resistance.
The general mechanism of action is that direct current flows through the proper electrolyte fluid
Where the anode is aluminum and another suitable metal is the cathode.
In this case, a thin layer of oxide is created on the aluminum surface, the thickness of which depends on various factors.
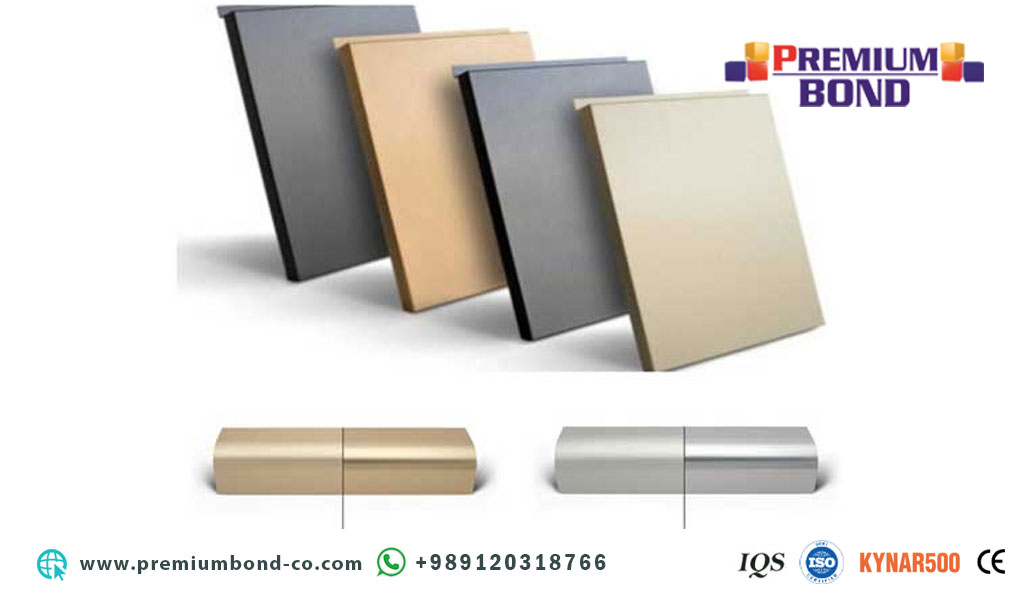
Aluminum parts and surfaces are analyzed for the following reasons:
A – Increased corrosion resistance:
- Oxide coating
Aluminum-flooded anodes protect the metal from corrosive agents and salts.
B – Increase the adhesion strength of colors:
- Oxide layer
Anode creates a chemically active surface and creates a suitable background for painting.
C – as one of the steps of plating:
- The porosity in the oxide coating
Anode increases the plating ability of aluminum parts. (For example, anodizing in phosphoric acid electrolyte can be used as a pre-plating step)
D – Create a suitable appearance for decoration and decorations:
- Oxide layer
The aluminum anode is naturally shiny and has good corrosion resistance. Therefore, it can be used as the final surface for decoration and decoration. The brightness and gloss of the surface depends on the type of alloy, the method of etching and polishing and other suitable conditions.
E- Insulation:
Aluminum oxide is insulated and can withstand insulators with voltages ranging from a few to several thousand volts, the quality and quantity of which depends on the type of alloy and the thickness of the oxide layer.
F – Increasing the ability of radiation and heat dissipation:
- Oxide layer
Anodes with thicknesses greater than 0.032 mm increase the radiation and heat dissipation capacity. For example, anodized aluminum sheet after painting with black can be used in a very desirable way to absorb heat up to about 230 degrees Celsius.
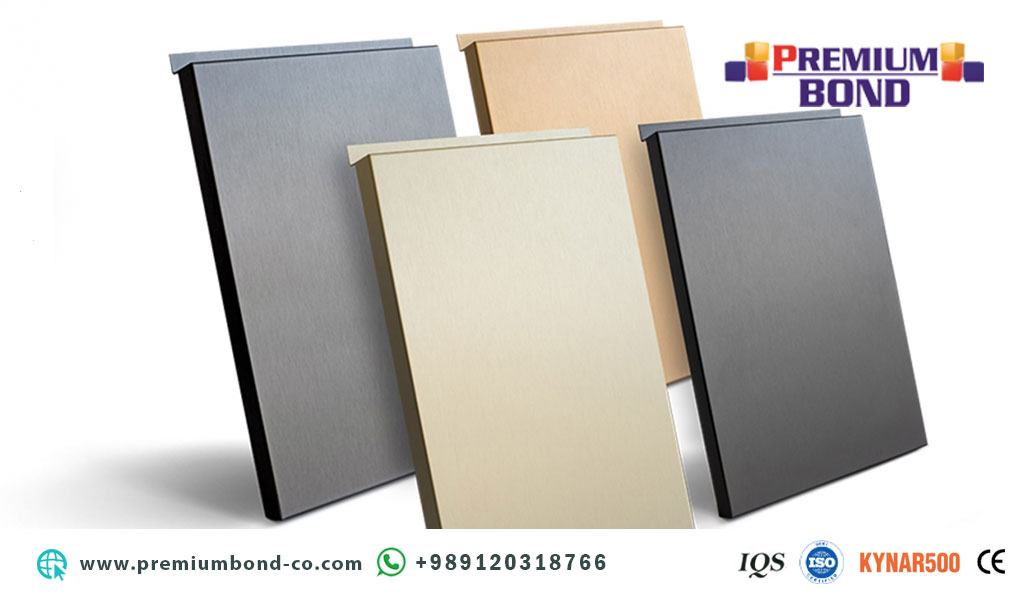
G – Increasing abrasion resistance:
Hard anodizing mechanism is created on aluminum parts with a thickness of about 1 to 4 mm, which has a high hardness and can be used to make bearings and rotating parts or other items that require abrasion resistance. Have used.
All oxide-anode coatings are harder than aluminum itself, but in some cases (such as the anode-anode oxidation layer in an acrochemical acid bath) they are soft and not suitable for use in situations where they require abrasion resistance.
During the aluminum anodizing process, aluminum can be made into beautiful colors and made beautiful and strong. As a result, a beautiful and attractive design is produced, the surface of which can be easily washed with hot water and does not need any cleaning and maintenance. It is naturally resistant to corrosion.
Leave a Reply